OVERVIEW
A Complete Honing Solutions Under One Roof
Abhi Fine Products, the industry's finest Honing Machine Manufacturer, an ISO 9001:2015 company, was established in 1996 with a passion to make a significant difference in the surface finishing industry. All these years, ABHI has been renowned as a successful Honing Machine Manufacturer, created a niche space for itself in the surface finishing industry by excelling in solving customer problems. Having set higher goals, we manufacture the Honing machines and honing tools by providing all the spares and testing the tool with the latest machineries and equipment installed in our in-house. Our speciality is making and testing all the processes of manufacturing at our in-house and the customer can get all the spares under one roof.
What we offer
A complete solution for your honing requirement, from the pioneers of Honing Machine Manufacturers, under one roof. Cutting-edge technologies are practised in the manufacturing of horizontal honing machines and vertical honing machines that enable our customers to have control over the higher precision and accuracy of the honing workpiece. Being one of the leading manufacturers of vertical honing machines, horizontal honing machines and honing tools, our machines add value to our customer's products with their salient features that supports them in practising fine honing works.
Our Facts
We strive to understand our clients and deliver to their needs.
Trusted by small & large brands, around the world.
Our core values
Our Happy Clients
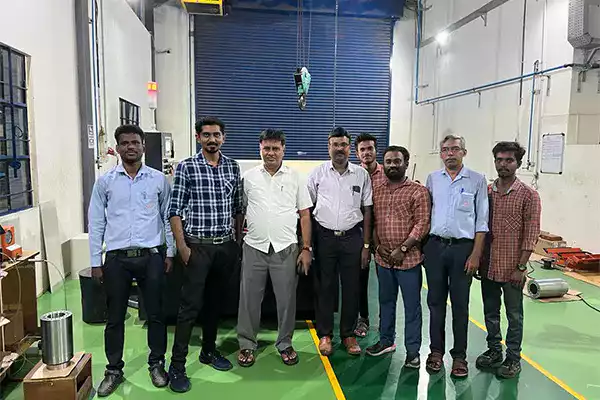
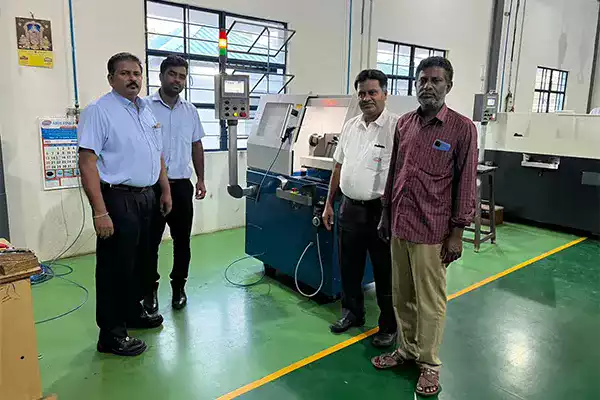
A complete one click solution for Single pass honing tool . As an Customer I feel from bottom of my heart that If Abhi Tools is accepted an order to achieve requirement with customer that's really an quality output. Fair enough to deal with them. the Its True. Please look the photo which is the latest product from Abhi Fine Products.
Sakthipriya Venkatesan
A Complete Solution for all your Honing Solutions. As an Employee I feel from bottom of my heart that If Abhi is Committed or accepted to achieve some requirement with the customer, without any deviation we are doing it for our customers. I am recording this information not just because I am an employee, Its True. Please look the photo which is the latest product from Abhi Fine Products.
Shameer Jan
Abhi fine products manufactures one of the finest honing machines that are on par with their imported counterparts. Abhi is always supportive to their Customers and Vendors
Saravanan
The CEO of this company is technically knowledgeable person. He provides solution to customers rather than selling the product.
Bharanitharan R