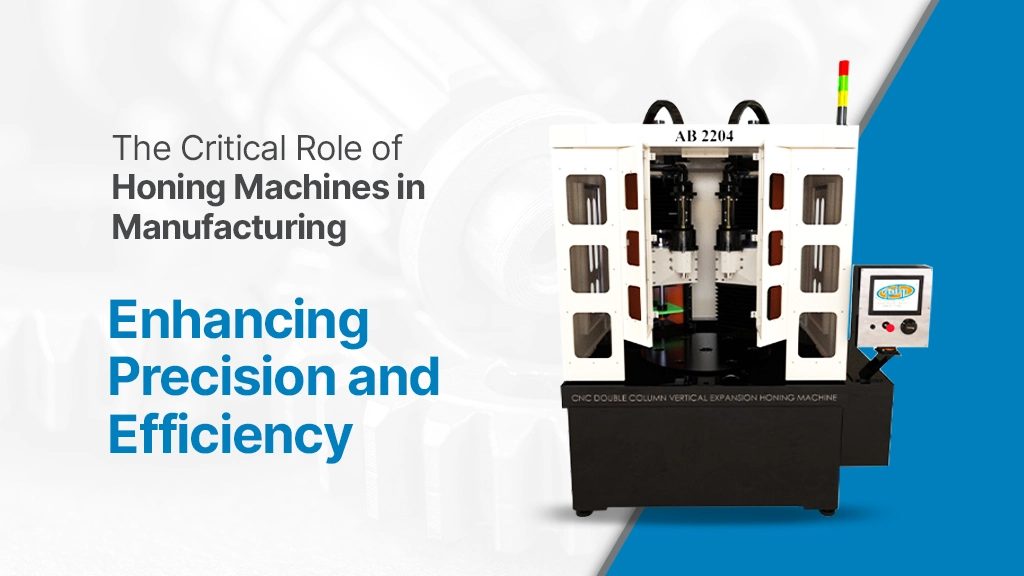
The Critical Role of Honing Machines in Manufacturing: Enhancing Precision and Efficiency
9 Oct, 2024
In the modern manufacturing environment, precision and efficiency are paramount. As industries eager to meet the ever-increasing demands for high-quality products, the importance of advanced machining processes cannot be overstated.
Among these processes,honing has emerged as a crucial technique, particularly in sectors where exacting tolerances and superior surface finishes are required. This article explains about the honing machines, exploring their role in manufacturing, their applications across various industries, and the tangible benefits they offer.
By examining actual facts and industry data, we will shed light on why honing machines are indispensable tools in today's manufacturing sectors.
Understanding the Honing Process
Honing is a metal removal technique that employs hard tools with super abrasive bonded stones or plated sleeves to correct
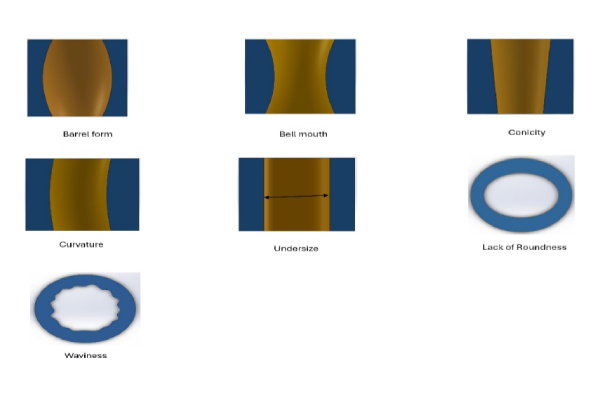
The honing process was developed to perfect bore geometry, control sizes, and achieve optimal surface finish and structuring. It provides the final sizing and imparts the desired surface pattern on internal bores. This is done using abrasive stones or sleeves of appropriate grit and grade, which are either rotated, reciprocated, or both, against the work surface under controlled pressure. By carefully combining rotation and reciprocation, the process can also create the desired crosshatch pattern on the honed surface.
Types of Honing Machines
Honing machines are broadly classified into two types: vertical and horizontal honing machines. Each type is suited to specific applications and offers unique advantages.
Vertical Honing Machines: Vertical honing machines are commonly used for large-scale production and are ideal for honing long cylindrical parts. These machines can produce highly accurate bores and are often employed in industries such as automotive, aerospace, and hydraulics. Vertical honing machines offer the advantage of being able to handle heavy workpieces and are known for their stability and precision. Additionally, there is two kinds of honing machines:
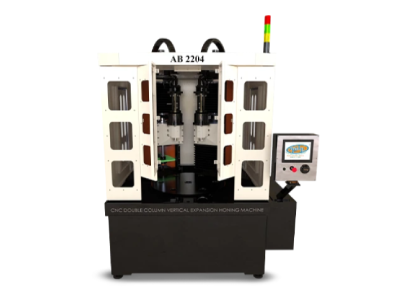
Single Pass Vertical Honing Machine
Single pass vertical honing machines are engineered to hone workpieces or components in one continuous operation. These machines are particularly effective for high-volume production, delivering consistent and accurate results.
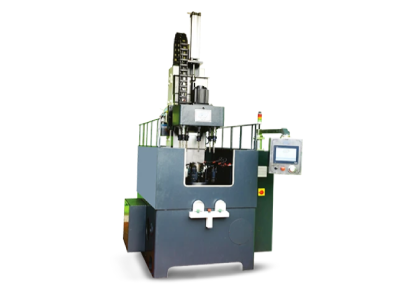
Features
- High Material Removal Rate: Single pass honing machines can remove material at rates ranging from 0.05 mm to 0.5 mm per pass, depending on the material and tool used. This efficiency is crucial for mass production environments.
- Vertical Design: The vertical configuration allows for gravity-assisted operations, which can help in the even distribution of honing fluid, promoting better cooling and lubrication during the honing process.
- Precision Stroke Control: Many machines are equipped with programmable logic controllers (PLCs) that allow for precise control over the stroke length and honing pressure, ensuring repeatable results within tolerances of ±0.005 mm.
- Versatility in Applications: Ideal for honing engine cylinders, hydraulic cylinders, and other cylindrical components, these machines can handle workpieces with diameters ranging from 20 mm to over 300 mm.
- Cooling and Filtration Systems: Integrated cooling systems maintain optimal temperature and viscosity of the honing fluid, which can improve the life of both the honing tool and the workpiece finish. Some models also include filtration systems that ensure the fluid remains clean, reducing wear and tear.
Expansion Vertical Honing Machine
Expansion vertical honing machines utilize expandable honing tools that can adapt to various diameters of workpieces or components, making them particularly useful for manufacturers who deal with components of differing sizes.
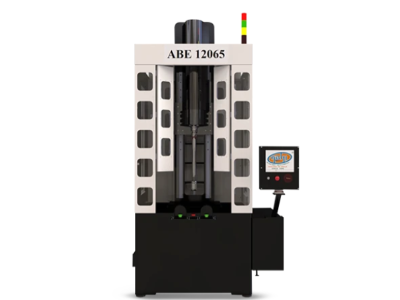
Features
Horizontal Honing Machines
Horizontal honing machines, on the other hand, are typically used for smaller workpieces and are well-suited for batch production. These machines are often used in the manufacture of gears, hydraulic valves, tubes for oil & gas industries and other precision components. Horizontal honing machines are valued for their originality and ease of operation, making them a popular choice in small to medium-sized manufacturing operations. One type of Horizontal Honing Machine is the Expansion Horizontal Honing Machine. It uses a horizontal orientation to perform honing operations, allowing for the refinement of large or heavy components with ease. These machines feature adjustable abrasive tools that expand to precisely control bore size and surface finish, making them particularly beneficial for handling intricate or sizable parts requiring high accuracy and surface quality.
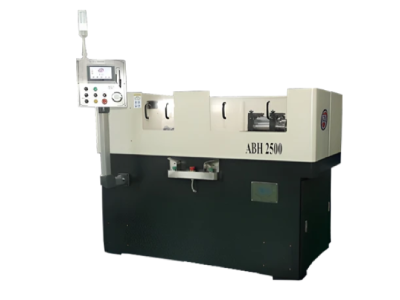
Applications of Honing Machines in Manufacturing
Honing machines find applications across a wide range of industries, each benefiting from the precision and surface finish improvements that the process offers. Some of the key sectors that rely on honing machines include:
1. Automotive Industry: The automotive industry is one of the largest users of honing machines. Engine components, such as cylinders, pistons, and connecting rods, require extremely precise bores to ensure optimal performance and longevity. Honing machines are used to achieve the desired bore size and surface finish, which are critical for maintaining compression and reducing wear in engines. According to industry data, the global automotive honing market is expected to grow at a CAGR of 8.2% from 2023 to 2030, driven by increasing demand for high-performance engines and the trend towards electric vehicles.
2. Aerospace Industry: In the aerospace sector, precision is paramount, and honing machines play a crucial role in manufacturing components that meet stringent tolerances. Aircraft landing gear, turbine blades, and hydraulic systems are just a few examples of parts that benefit from honing. The process ensures that these components have the necessary surface finish and dimensional accuracy to withstand the extreme conditions of flight. The use of honing machines in the aerospace industry is expected to increase as the demand for fuel-efficient and lightweight aircraft continues to rise.
3. Hydraulic and Pneumatic Systems: Hydraulic and pneumatic systems rely on components with precise bores and smooth surfaces to function efficiently. Honing machines are used to manufacture cylinders, valves, and pumps that are essential for these systems. The ability of honing machines to produce bores with tight tolerances and excellent surface finishes ensures that hydraulic and pneumatic systems operate with minimal friction and leakage, improving their overall performance and reliability.
4. Oil and Gas Industry: The oil and gas industry require components that can withstand harsh operating environments and high pressures. Honing machines are used to produce precision components such as drilling tools, valves, and pumps that are critical for exploration and production activities. The durability and reliability of these components are enhanced by the honing process, which ensures that they meet the required specifications for size, shape, and surface finish.
5. Medical Device Manufacturing: The medical device industry demands high levels of precision and cleanliness in the manufacturing of components such as syringes, implants, and surgical instruments. Honing machines are used to produce these components with the required accuracy and surface finish, ensuring that they meet the stringent standards set by regulatory bodies. The global medical device market is projected to grow significantly in the coming years, further driving the demand for honing machines in this sector.
Advantages of Using Honing Machines
Honing machines offer several advantages that make them indispensable in modern manufacturing. Some of these advantages, which are exclusive to Abhi Fine Products honing machines, will be mentioned as (only available):
1. Improved Surface Finish: Honing machines are capable of producing exceptionally smooth surfaces, which are critical for reducing friction, wear, and tear in mechanical components. The process also helps to eliminate surface imperfections such as scratches and chatter marks, resulting in a superior surface finish.
2. Mass Production: All the mass production movements reciprocating, rotation, are automatically operated by servo motor, this provides high accuracy, convenient operation and greatly upgrades productivity. Also, it is excellent for mass production as well as small quantities, and flexible component honing.
3. Safe To Use (only available): Some of the machines have more than 30 alarms to alert the operators which shows us the honing machine is safe for us to use.
4. Pecking Operations (only available): In the blind bore honing process, using pecking operation to effectively remove the taper at the bottom of the component. This ensures precise results and a smooth bore surface.
5. Adjustable Feed Rate and RPM (only available): Depending on the specific position within the bore, machines can adjust the feed rate and rotational speed; by varying these parameters, we optimize the honing process for different areas of the bore.
6. Energy Saving (only available): Some of the machine is designed to deliver maximum performance while maintaining minimal power consumption, making it an eco-friendly choice for sustainable operations.
7. Auto Gauging (only available): The Part Verification after a precise Machining operation can be done with the help of auto gauging arrangement.
8. Enhanced Dimensional Accuracy: The ability to achieve tight tolerances is one of the key benefits of honing machines. This is particularly important in industries where even the slightest deviation from specified dimensions can lead to performance issues or component failure. Honing ensures that parts meet the required dimensional accuracy, improving their functionality and reliability.
9. Extended Component Life: By producing parts with precise bores and smooth surfaces, honing machines help to extend the life of components. This is because the improved surface finish reduces friction and wear, leading to longer-lasting parts. In industries such as automotive and aerospace, where component longevity is critical, the use of honing machines can lead to significant cost savings over time.
10. Consistency and Repeatability: Honing machines are designed to deliver consistent results, even in high-volume production environments. This repeatability is essential for maintaining quality and ensuring that every component meets the required specifications. In industries where uniformity is critical, such as automotive and medical device manufacturing, the ability to produce identical parts consistently is a significant advantage.
Challenges and Considerations in Honing
Honing presents several challenges and considerations that must be addressed to ensure optimal results. Key issues include:
1. Tool Wear: Abrasive stones or sleeves can wear down over time, which affects the consistency and quality of the honing process. For example, studies show that tool wear can lead to dimensional deviations of up to 0.005 mm if not regularly monitored and replaced. Effective tool maintenance and replacement schedules are crucial for maintaining precision.
2. Bore Geometry: Achieving precise bore geometry requires careful control of honing parameters. Research indicates that variations in honing speed, pressure, and abrasive grit can result in deviations in bore dimensions. For instance, a study by the Society of Manufacturing Engineers found that incorrect honing parameters could lead to geometric deviations of up to 0.01 mm, impacting the final fit and function of components.
3. Heat Generation: Honing generates heat, which can cause thermal distortion if not managed properly. Effective cooling and lubrication are essential to prevent overheating. Data from industry sources indicate that excessive heat can lead to a thermal expansion of the bore, resulting in dimensional inaccuracies. Maintaining proper coolant flow and temperature control can mitigate these effects.
4. Material Compatibility: Different materials respond differently to honing. For example, materials like cast iron and steel require different abrasive types and honing parameters. A study from the Journal of Materials Processing Technology highlights that using the wrong abrasives or parameters can result in poor surface finishes and reduced tool life, emphasizing the need for material-specific honing techniques.
5. Machine Calibration: Proper calibration of honing machines is critical for maintaining accuracy and consistency. Regular maintenance and adjustments are necessary to ensure that equipment operates within specified tolerances. Industry guidelines suggest that regular calibration checks can prevent deviations and maintain dimensional accuracy within 0.002 mm.
By addressing these challenges with factual insights and industry practices, manufacturers can optimize the honing process and achieve high-quality, precise components.
Conclusion
Honing Machines are essential tools in the Manufacturing Industry, providing the precision and surface finish needed to produce high-quality components. Their applications span a wide range of industries, from automotive and aerospace to medical device manufacturing, highlighting their originality and importance. While there are challenges associated with using honing machines, the benefits they offer in terms of improved surface finish, enhanced dimensional accuracy, and extended component life make them indispensable tools in modern manufacturing.
As Industries continue to evolve and demand higher levels of precision and efficiency, the role of Honing Machines is likely to become even more significant. Manufacturers who invest in Honing Technology and skilled labour will be well-positioned to meet the challenges of the future and maintain a competitive edge in the global market. With the right approach, honing machines can help manufacturers achieve their goals of producing high-quality products that meet the exacting standards of today's Industries.
Tell us how can we assist you?
We are always happy to answer any questions!
Just fill in the form and we will get back to you.
© 2025 All rights reserved. Abhi Fine Products.
Designed & Developed by Appac Mediatech Pvt Ltd