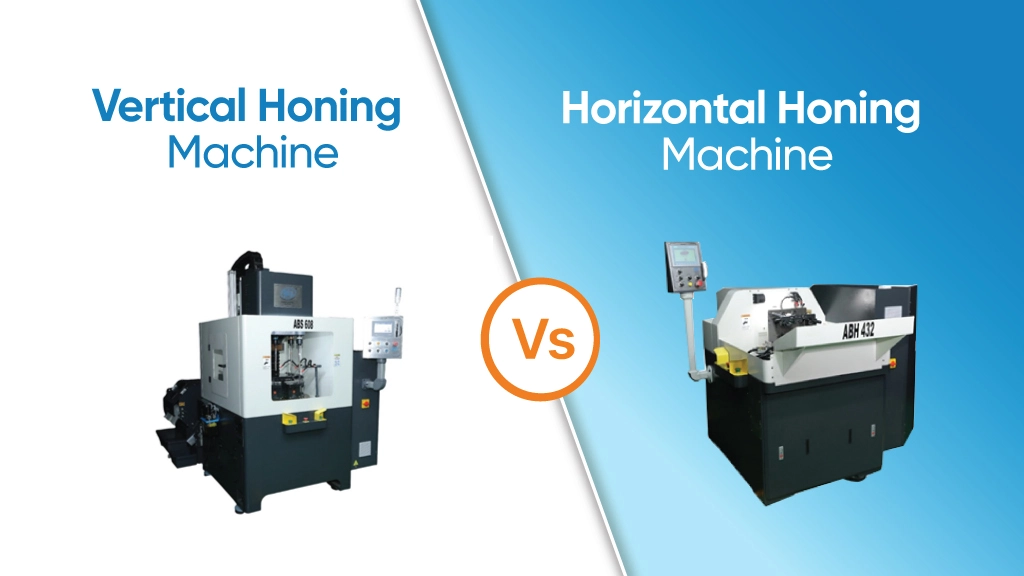
Vertical Honing Machine vs Horizontal Honing Machine
14 Sep, 2024
Introduction to Honing Machines
In precision manufacturing, honing is essential to the process for ensuring the dimensional accuracy and surface quality of cylindrical and other bore-shaped components. Honing is a machining process that uses an abrasive tool to remove material and improve the geometry of parts, delivering smooth, accurate surfaces. The hone process was developed to achieve the perfection in bore geometry, size control, surface finish and surface structuring. The honing process provides the final sizing and creates the desired finish pattern on the inner bores. The stones or sleeves are rotated or reciprocated or both in the part with hone abrasive under controlled pressure. A controlled Combination of rotation and reciprocation can also produce the desired cross-hatch pattern in the surface of the part being honed. It’s commonly employed in industries such as automotive,aerospace, and manufacturing, where high-precision finishes are essential.
Honing machines come in different configurations, with vertical and horizontal honing machines being the two primary types. Each of these machines has unique advantages and disadvantages,making them suitable for specific applications. In this article, we will compare vertical honing machines with horizontal honing machines, focusing on their mechanisms, applications, and the factors that can guide professionals in choosing the best option for their needs.
How Vertical Honing Machines Work
Vertical Honing Machines Are Typically Designed for Large Workpieces or components that require precision honing of long bores. They operate by moving the honing tool vertically within the component. The honing tool expands and contracts, allowing the abrasive stones to contact the internal surface of the bore. The up-and-down motion ensures a smooth and consistent honing process. There are two options: either a floating tool or a fixed float, depending on the component, to maintain alignment between both the tool and component axis.
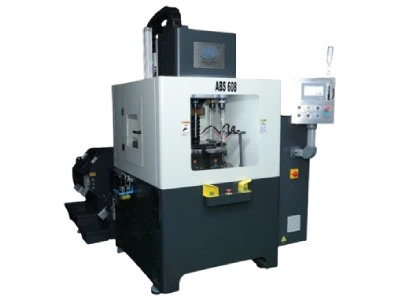
Mechanism
In a vertical honing machine, the component is securely fixed while the honing tool moves vertically.This vertical movement, combined with rotary motion, creates the necessary cutting action to remove material from the internal surface. The machine typically allows for adjustments in speed, pressure, and feed rate to achieve the desired finish and dimensional accuracy. For mass production,a Fibro rotary table can be used for loading and unloading without stopping the honing process.
Applications
Vertical honing machines are ideal for deep bores and longer components, such as cylinder liners,valves, and gears. Heavier components are bored exclusively using vertical honing machines. Their ability to handle heavy workpieces and long strokes makes them the preferred choice in industries requiring high precision for long bores, such as the automotive and hydraulic sectors.
Advantages
How Horizontal Honing Machines Work
Horizontal Honing Machines Are Designed for Shorter Bores and Are Often Used for batch production tasks. The honing tool in this type of machine moves horizontally through the component, which is often rotated or held stationary depending on the setup. Horizontal honing machines excel in honing shorter cylindrical components.
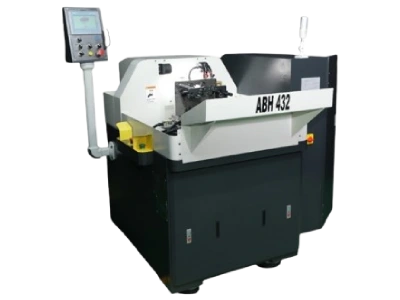
Mechanism
In a horizontal honing machine, the honing tool passes horizontally through the bore of the component, which is either held in place or rotated. Like vertical machines, the honing stones expand and contract to remove material and refine the surface finish. Horizontal honing is typically faster because the machines are generally smaller and handle smaller components.
Applications
Horizontal honing machines are used for shorter bores, making them ideal for components such as bushes, sleeves, and puppet components. These machines are well-suited for high-speed production and often find applications in automotive and industrial manufacturing.
Advantages
Space Requirements
Vertical honing machines require significantly more vertical space due to the up-and-down motion of the honing tool. They are generally larger and take up more room, making them ideal for facilities with ample vertical clearance. On the other hand, horizontal honing machines have a more compact design, requiring less space. For smaller workshops or manufacturing plants with limited space,horizontal machines may be the more practical option.
Productivity and Efficiency
Horizontal honing machines are generally faster when it comes to honing shorter components. Their design allows for quicker cycle times and higher throughput in batch production settings. Vertical honing machines, while typically slower, offer greater precision and control, especially for long bores. This makes vertical machines more efficient in applications where precision and accuracy are critical, even if the honing process takes longer.
Precision and Accuracy
Vertical honing machines are known for delivering superior precision, particularly in deep or long bores. The ability to control the honing tool’s movement in a vertical direction allows for greater accuracy in larger components. Horizontal honing machines, while still capable of achieving high precision, may not match the level of accuracy provided by vertical machines for certain applications, especially in longer bores.
Cost Factors
In terms of cost, horizontal honing machines tend to be more affordable, both in initial investment and operational costs. They are smaller, consume less energy, and are easier to maintain. Vertical honing machines, being larger and more complex, often come with a higher price tag. However, the increased cost may be justified by their ability to handle larger and more demanding components,especially for precision jobs.
Choosing the Right Machine for Your Application
Selecting between a vertical or horizontal honing machine depends on several factors, including the type of material being worked on, production scale, accuracy requirements, and available space.
Type of Material and Workpiece
If you are working with larger, heavier components that require deep bore honing, such as cylinders or long shafts, a vertical honing machine is likely the better option. The vertical configuration handles long workpieces more effectively and delivers better precision in these scenarios.
For smaller, shorter workpieces, such as gears, valve bodies, or small engine components, a horizontal honing machine offers a more efficient solution. Horizontal machines are faster, and their compact size makes them ideal for facilities with limited space.
Production Scale
For high-volume production environments, where speed and efficiency are critical, vertical honing machines are often the best choice. Their faster cycle times make them ideal for mass production of shorter components. In contrast, Horizontal honing machines are better suited for lower-volume, moderate-precision jobs where there is a requirement of faster honing.
Precision and Accuracy Needs
If your application requires extremely high precision, particularly in long bores, a vertical honing machine will offer better results. For applications that demand less precision and focus on production speed, a horizontal honing machine will suffice.
Industry Recommendations
Automotive industry: Both vertical and horizontal honing machines are useful, but vertical machines are better for honing engine cylinders and deep components, while horizontal machines excel in honing gears and smaller engine parts.
Hydraulic and aerospace sectors: Vertical honing machines are often preferred for their precision in handling large and complex components.
General manufacturing: Horizontal honing machines are commonly used for the mass production of small and mid-sized components that are also lower in weight.
Key Differences:
Features | Vertical Honing Machine | Horizontal Honing Machine |
Orientation | Vertical setup for irregular or heavy-weight components | Horizontal setup for smaller components |
Applications | Engine blocks, crankshafts | Connecting rods, transmission parts |
Precision | Higher precision due to vertical stability | Slightly precise but flexible |
Automation | More automated options | Manual, semi-automatic or automatic |
Cost | Component fixation is more expensive compared to a horizontal honing machine | More cost-effective for small operations |
Maintenance | Requires specialized maintenance | Easier to maintain with lower costs |
Weighing Precision and Productivity in Honing Machine Selection
In the end both vertical and horizontal honing machines have their unique strengths and are designed for different types of applications but both the machine has PLC (Programmable Logic Controller) to control and HMI (Human Machine Interface) to interface the machine operations. Vertical honing machines excel in handling larger, heavier components with long bores and offer higher precision, making them suitable for industries where accuracy is essential. Horizontal honing machines, on the other hand, are faster and more cost-effective for shorter workpieces, making them ideal for mass production environments. Both machines have Double Index Table options for increased production, with an option of automatic clamping and de-clamping for fixtures.
When choosing between these two types of honing machines, professionals should consider factors such as space, productivity needs, precision requirements, and the nature of the components being worked on. By carefully evaluating these factors, manufacturers can select the right machine that will meet their production goals and deliver the desired results.