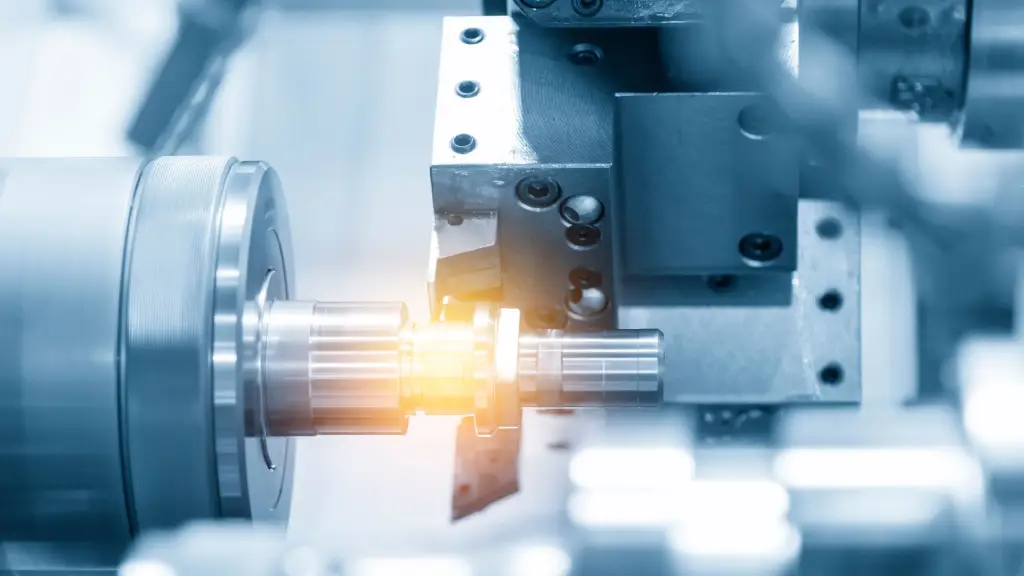
Why Honing Is Preferred For Manufacturing Critical Parts And Components
18 Aug, 2023
Honing solutions are creating a greater impact in the industry. The newer discoveries of the machine's cutting-edge, functional parts and other critical components paved the way for developing products of complex engineering designs.
Starting from the prototype to the finished product, precision and accuracy are primary requirements playing a significant role in product development. Honing products contributed to the industrial revolution.
"Compact" is the most preferred and demanding feature of customers from different industries. The simplification of the product dimension holistically results in the invention of small-sized parts and components.
At the same time, the functioning of the machine should be ensured without any drop in efficiency. Also, when developing a newer version of the product, the parts add-on to deliver compactness.
The drop in accuracy at any assembled part affects the cumulative performance. Honing is the primary solution to enhance the accuracy of the parts.
Honing
Honing is the process of uplifting the surface finishing and geometry of the machining part. The manufacturing of critical parts within the specified tolerance level is quite challenging.
Though the conventional method of grinding, machining, boring, and drilling is still in practice, honing has outperformed the existing manufacturing techniques.
The products, parts, and components machined with honing ensure the parts are within the tolerances, which is very challenging to retain in the bulk production of the parts machined with the conventional manufacturing methods.
Every part and component integrated into the final product relies on the associated product parts and components. Typically, honing manufacturing techniques is highly preferred in manufacturing critical parts and components.
The critical part contributes to the major functioning of the product, which is dependent on other assembled products.
Hence, today's world has no high-performance compact products with no honing process.
Industries
Honing machines are the trendsetter in the manufacturing industry. The excellence of the end product is the outcome of honing integrated solutions when developing/manufacturing the parts and components.
Many industries Honing machines have replaced the practice of conventional manufacturing techniques. But, in particular, it has significantly impacted the automobile and aerospace industries.
Automobile industries involve the assembly of various critical components and parts. The assembly of engine parts is challenging. Even a small misplacement of the assembled part makes a big difference and causes functional inefficiency. Honing machines allow the operator to control the engine parts' precision and accuracy.
Also, compared to conventional machining processes, honing tools produce defect-free critical components and parts in large quantities.
Quality Over Quantity
Compared to other manufacturing techniques, honing incurs higher operating time. Hence, the production capacity and throughput are lesser than other machining processes. Automobile and aerospace industrial products are highly valued products
Hence, compromising the quality of the products leads to huge losses affecting the firm's profitability. Due to these reasons, though the production rate of the honing machine is reasonable, they are highly preferred to minimize the incurring loss.
With consistent modifications and improvements, the honing machines can match the production capacity as planned to deliver the machined products within the deadline. The precision and accuracy are highly assured at each stage of the honing production.
Hence, quality over quantity has been the best strategy to increase the firm's ROI. In addition, though the production volume of high-value products is low, the margin will be greater.
The stability and upscaling of the trendline are assured with honing machines
Honing and Material Type
Honing has the greatest advantage of machining any workpiece material, irrespective of its hardness. The pressure applied during the machining process under boring and grinding conditions affects the workpiece.
The chances of deformation in the workpiece are higher. The machining plan differs at various points of the workpiece. Therefore, the operator has to be conscious throughout the machining process to machine the workpiece within the tolerance level.
This is not the case with the honing operation. Abrasive materials such as diamonds and other abrasive stones are used to machine the surface finish or bore the diameter at the defined spindle rpm without resting additional pressure on the workpiece during the machining process.
Various geometry planned and designed in the single workpiece can be machined without exceeding tolerances with higher precision.
Lubricants
Honing operations are carried out at a low speed compared to other machining operations. The heat generated during the machining is less than the uncertain accidents and machining errors. The special need for lubrication is eliminated to machine all types of material hardness as the machine runs low spindle speed.
The Bottom Line
Honing machines have greater advantages and higher preference in particular machining applications. If you're interested in knowing more about the honing process, its machine types, and other special features, then Abhi Fine Products is one of the industry's leading manufacturers offering marvel Honing solutions. Please visit Abhi Fine Products to connect with industry experts.