Understanding the Honing Process: A Key to Precision Machining
19 Mar, 2025
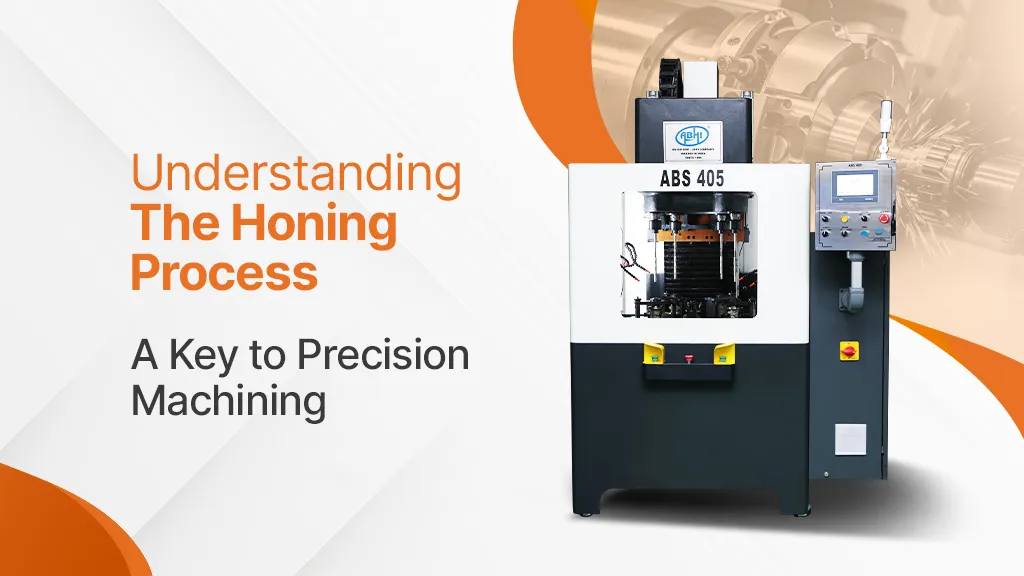
What is Honing?
Honing is a controlled material removal process that utilizes abrasive stones to refine the surface of a workpiece. It is primarily used for finishing internal cylindrical surfaces, ensuring a high level of accuracy in terms of roundness, straightness, cylindricity and surface texture. The process involves a rotating tool with bonded abrasive stones that move in a controlled reciprocating motion against the bore's surface, achieving a consistent and precise finish. This process is widely employed in industries such as automotive, aerospace, hydraulics, and manufacturing, where precision is paramount.
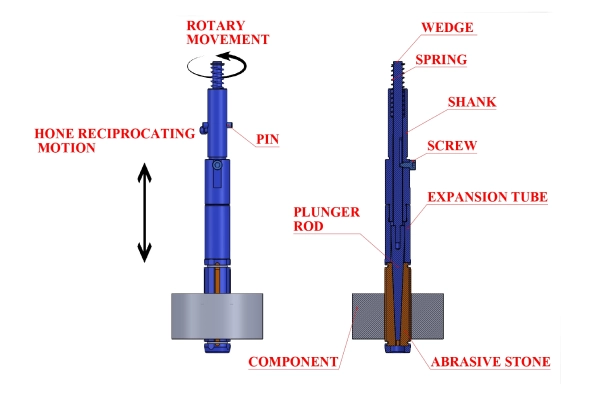
Expansion Honing
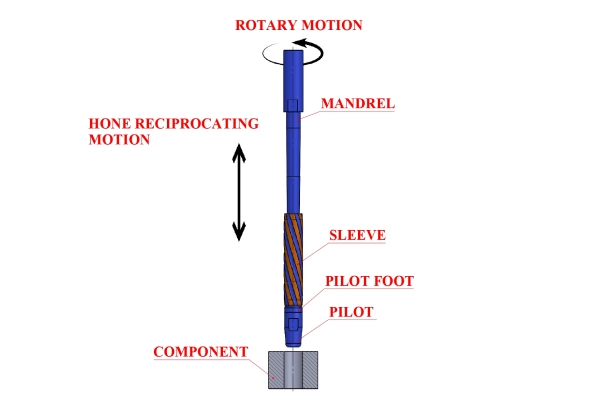
Single Pass Honing
How the Honing Process Works
The honing process consists of the following key steps:
- Workpiece Preparation: The component to be honed is secured in place, ensuring stability during the process.
- Abrasive Tool Engagement: A honing tool, equipped with abrasive stones, is introduced into the bore.
- Reciprocating and Rotating Motion: The honing tool moves back and forth while rotating, creating a cross-hatched pattern that enhances lubrication retention and wear resistance.
- Material Removal: Controlled pressure and speed allow for gradual material removal, refining the bore to the desired specifications.
- Final Inspection: Once the honing cycle is complete, the workpiece is measured to ensure it meets the required tolerances and surface quality.
Advantages of Honing
Honing offers several advantages over other finishing processes, including:
- Superior Surface Finish: Produces high-quality, smooth, and uniform surfaces with low roughness values.
- Enhanced Dimensional Accuracy: Achieves precise control over bore size, roundness, cylindricity and straightness.
- Improved Wear Resistance: The cross hatch pattern enhances lubricant retention, reducing wear and increasing component lifespan.
- Inventiveness: Suitable for a wide range of materials, including steel, cast iron, aluminium, and ceramics.
Applications of Honing
The honing process is widely used in various industries for different applications, such as:
- Automotive Industry: Cam, Crank shaft, Liner, Piston, Piston rings, Connecting rod, Yoke, Engine cylinders, fuel injectors, cylinder liner and transmission components.
- Aerospace Sector: Hydraulic cylinders, landing gear components, and turbine parts.
- Hydraulics and Pneumatics: Precision honing of hydraulic, flow control valve, manifold, spools, direction control valve, sleeves and pneumatic cylinders.
- Medical Equipment: High-precision honing for surgical instruments and implants.
Lapping vs. Honing: Understanding the Differences
Lapping and honing are both precision surface finishing processes used to improve dimensional accuracy, surface finish, and geometric perfection. While they share some similarities, they are distinct in terms of technique, applications, and results. Understanding the differences between these two processes can help manufacturers select the best method for their specific requirements.
What is Lapping?
Lapping is a surface finishing process that involves using a loose abrasive slurry or compound between two surfaces to achieve ultra-fine finishes and precise flatness. The process is typically performed on flat surfaces but can also be applied to cylindrical components.
How Lapping Works
- Preparation: The workpiece is placed between a rotating lap plate and a conditioning ring or another surface.
- Abrasive Slurry Application: A fine abrasive slurry (such as diamond, aluminium oxide, or silicon carbide) is introduced to the interface.
- Relative Motion: The workpiece moves in a controlled manner while the lap plate rotates, distributing the abrasive particles evenly.
- Material Removal: The abrasive particles gradually wear down high points on the surface, improving flatness and smoothness.
- Final Inspection: The surface is checked for desired finish and dimensional accuracy.
Applications of Lapping
- High-precision flat components such as optical lenses, semiconductor wafers, and gauge blocks.
- Sealing surfaces in valves and mechanical seals.
- Automotive and aerospace industries for precision gears and engine components.
- Bearing and piston rings for achieving extremely fine finishes.
Key Differences Between Lapping and Honing
Feature | Lapping | Honing |
---|---|---|
Process Type | Free abrasive process | Bonded abrasive process |
Material Removal | Minimal and gradual | Controlled stock removal |
Application | Flat and sometimes cylindrical surfaces | Internal cylindrical bores |
Abrasive Medium | Loose abrasive slurry | Bonded abrasive stones |
Surface Finish | Extremely fine (sub-micron level) | Smooth with cross hatch pattern |
Typical Industries | Optical, semiconductor, automotive | Automotive, aerospace, medical |
Common Tools | Lapping plates, conditioning rings | Honing mandrels, honing stones |
Honing vs. Grinding: Key Differences and Applications
Honing and grinding are both material removal processes used in manufacturing to achieve high precision and superior surface finishes. While they serve similar purposes, they differ significantly in their methods, applications, and results. Understanding these differences can help manufacturers choose the best process for their needs.
What is Grinding?
Grinding is a material removal process that uses an abrasive wheel to cut and smooth surfaces. It is widely used for shaping, finishing, and achieving tight tolerances in both cylindrical and flat workpieces.
How Grinding Works
- Workpiece Setup: The component is securely clamped or held in a fixture.
- Abrasive Wheel Engagement: A rotating grinding wheel contacts the workpiece surface.
- Material Removal: High-speed rotation of the abrasive wheel removes excess material.
- Cooling and Lubrication: Coolants are often used to prevent overheating and maintain surface integrity.
- Final Inspection: The workpiece is measured to ensure it meets dimensional and finish requirements.
Applications of Grinding
- Finishing of hardened metal components like gears and shafts.
- Surface grinding of flat components in tool and die making.
- High-precision cylindrical grinding for bearing and spindle components.
- Removal of excess material in mass production environments.
Key Differences Between Honing and Grinding
Feature | Honing | Grinding |
---|---|---|
Process Type | Low-speed, controlled material removal | High-speed, aggressive material removal |
Material Removal | Small, precise stock removal | High stock removal rate |
Application | Internal cylindrical bores | External and flat surfaces |
Abrasive Medium | Bonded abrasive stones | Abrasive grinding wheel |
Surface Finish | Smooth with cross hatch pattern | Fine to ultra-fine finish |
Typical Industries | Automotive, aerospace, medical | General machining, tool & die, manufacturing |
Common Tools | Honing mandrels, honing stones | Grinding wheels, surface grinders |
Honing vs. Burnishing: Key Differences and Applications
Honing and burnishing are both surface finishing processes used in manufacturing to enhance dimensional accuracy and surface quality. While they serve similar purposes, they differ significantly in their methods, applications, and results. Understanding these differences can help manufacturers choose the best process for their needs.
What is Burnishing?
Burnishing is a finishing process that improves surface quality and hardness by using a rolling or pressing tool to deform the material plastically without removing material. The process enhances surface finish and increases wear resistance by creating a smooth and hardened surface.
How Burnishing Works
- Workpiece Setup: The component is securely positioned in a machine or fixture.
- Burnishing Tool Engagement: A hardened roller or ball tool is pressed against the surface.
- Plastic Deformation: The pressure causes surface material to be redistributed, smoothing out imperfections.
- Surface Hardening: The process improves surface hardness, reducing wear and increasing fatigue resistance.
- Final Inspection: The component is measured to ensure the desired finish and hardness are achieved.
Applications of Burnishing
- Automotive crankshafts and camshafts for enhanced durability.
- Hydraulic and pneumatic cylinders for improved sealing surfaces.
- Aerospace landing gear components requiring high wear resistance.
- Medical implants and surgical tools demanding ultra-smooth surfaces.
Key Differences Between Honing and Burnishing
Feature | Honing | Burnishing |
---|---|---|
Process Type | Abrasive material removal | Plastic deformation without material removal |
Material Removal | Small, precise stock removal | No material removal |
Application | Internal cylindrical bores | External and internal surfaces |
Tool Type | Bonded abrasive stones | Rollers, balls, or pressing tools |
Surface Finish | Smooth with cross hatch pattern | Highly polished and hardened surface |
Typical Industries | Automotive, aerospace, medical | Automotive, aerospace, medical, hydraulic |
Common Tools | Honing mandrels, honing stones | Burnishing rollers, balls, or diamond tools |
Types of Honing Tools and Their Applications
Honing is a precision machining process used to improve the surface finish, roundness, and dimensional accuracy of cylindrical bores. The efficiency of the honing process depends on the type of honing tool used. Honing tools vary based on their design, abrasives, and applications. Understanding these tools helps in selecting the right one for specific machining needs.
Single-Pass Honing Tools
Single-pass honing tools use fixed-diameter super abrasive sleeves instead of expandable stones. These tools are designed for high-precision applications and provide excellent repeatability.
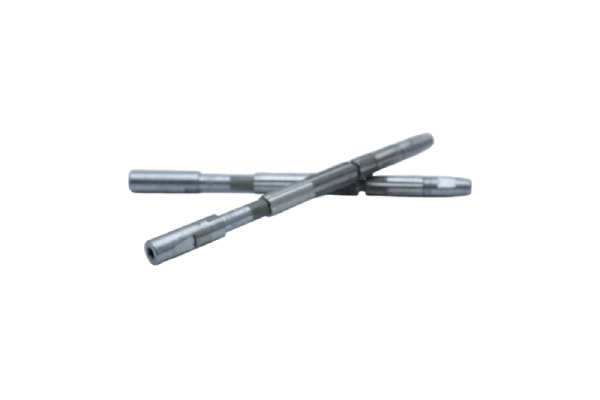
Single – Pass Honing
Applications:
- Aerospace and automotive industries for engine components.
- High-precision hydraulic and pneumatic cylinders.
- Medical and surgical instruments requiring ultra-precise bores.
Expandable Honing Tools
Expandable honing tools feature adjustable abrasive stones that expand and contract to fit different bore sizes. These tools allow gradual stock removal and provide a superior surface finish.
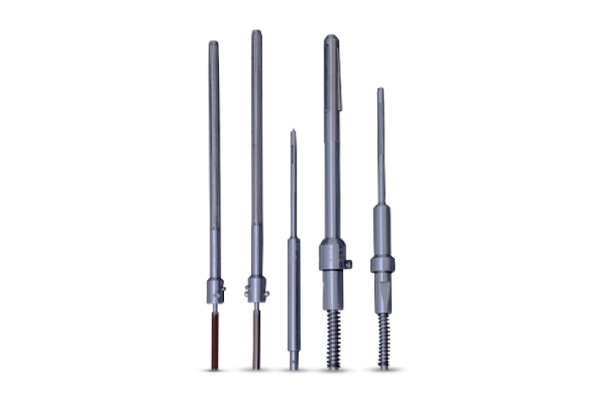
Expansion Honing
Applications:
- General machining and repair work.
- Automotive cylinder blocks and liners.
- Industrial equipment with varied bore sizes.
Diamond and CBN Honing Tools
Diamond and Cubic Boron Nitride (CBN) honing tools use super abrasives to enhance precision and durability. These tools are ideal for machining hard materials and achieving superior surface finishes.
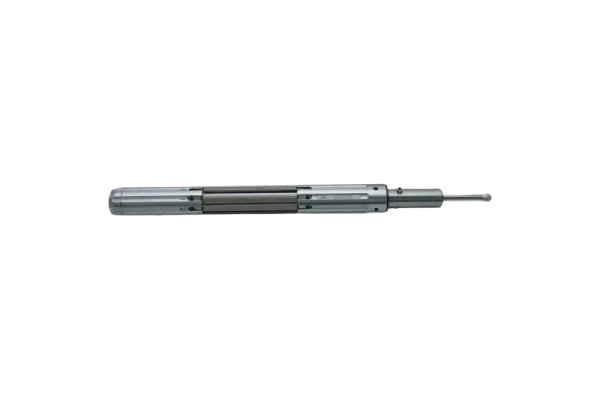
CBN Honing
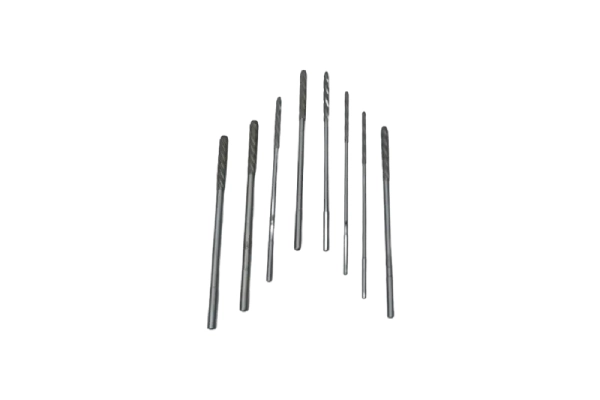
Diamond Honing
Applications:
- High-hardness alloys and ceramics.
- Aerospace and defence components.
- High-wear industrial parts requiring long tool life.
Plateau Honing Tools
Plateau honing tools are designed to create a cross-hatched surface finish, which improves oil retention and reduces friction. This type of honing tool is commonly used in applications requiring lubrication.
Applications:
- Automotive and diesel engine cylinders.
- Hydraulic components needing extended service life.
- Industrial applications requiring controlled lubrication.
Flexible Honing Brushes (Ball Hones)
Flexible honing brushes, also known as ball hones, are composed of abrasive globules mounted on a flexible shaft. These tools are effective for deburring and finishing small- diameter bores.
Applications:
- Deburring and finishing hydraulic and pneumatic tubes.
- Cleaning and maintaining engine cylinders.
- Small-diameter applications in medical and aerospace industries.
Mandrel Honing Tools
Mandrel honing tools use a series of honing stones mounted on a mandrel. These tools expand outward to engage with the bore walls, ensuring uniform material removal and high accuracy.
Applications:
- Precision honing of gear and bearing bores.
- Improving roundness in industrial components.
- High-precision bore finishing in automotive parts.
Choosing the Right Honing Tool
Selecting the appropriate honing tool depends on factors such as:
- Material hardness and type.
- Required surface finish and bore accuracy.
- Production volume and precision demands.
- Lubrication and wear resistance needs.
Types of Honing Fixtures and Their Applications
Honing fixtures are essential components in the honing process, providing stability, precision, and consistency while machining bores to achieve the desired surface finish and accuracy. The choice of honing fixture depends on the workpiece material, size, shape, and application requirements.
Standard Workpiece Holding Fixtures
Standard honing fixtures are commonly used for general machining applications. These fixtures securely hold cylindrical or rectangular workpieces, ensuring stability during the honing process.
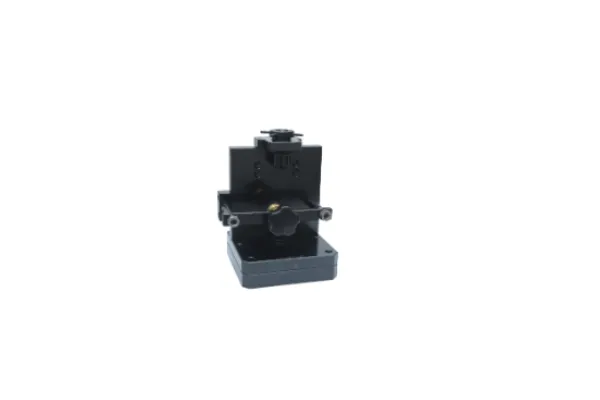
Applications:
- Automotive and aerospace engine components.
- General manufacturing requiring consistent bore finishing.
- Industrial machinery parts with standard bore dimensions.
Custom Honing Fixtures
Custom honing fixtures are designed to accommodate unique workpiece shapes, sizes, or materials. They provide high-precision alignment and optimal stability for specialized applications.
Applications:
- Complex hydraulic and pneumatic components.
- Medical and surgical instruments with precise bore requirements.
- Aerospace components requiring tight tolerances.
Self-Centering Fixtures
Self-centering honing fixtures automatically adjust to the workpiece, ensuring uniform pressure and alignment during the honing process. This feature helps in achieving accurate and consistent bore dimensions.
Applications:
- High-precision automotive and aerospace parts.
- Bearings, gears, and transmission components.
- Workpieces with varying bore sizes requiring uniform machining.
Floating Fixtures
Floating honing fixtures allow controlled movement of the workpiece during honing, ensuring even material removal and reducing the risk of bore distortion.
Applications:
- Long and slender bores requiring uniform honing.
- High-precision applications in medical and defence industries.
- Hydraulic cylinder components demanding concentricity.
Types of Floating Fixtures:
Radial Floating Fixture
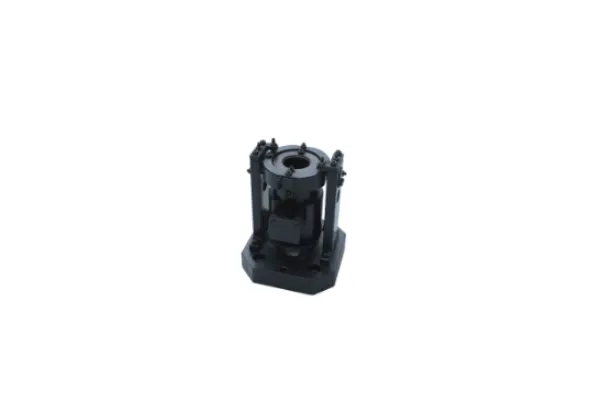
A radial floating fixture allows movement in a radial direction, enabling the honing tool to self- align with the bore. This ensures even pressure distribution and compensates for any misalignment between the tool and the workpiece. Radial floating fixtures are ideal for applications where the bore position may vary slightly but remains within a specified tolerance.
Axial Floating Fixture
Axial floating fixtures allow movement in the axial direction, accommodating variations in bore alignment along the tool's length. This type of floating fixture helps in achieving consistent surface finish and dimensional accuracy, especially in deep honing applications where the tool must adapt to slight misalignments in the axial direction.
Radial & Axial Floating Fixture
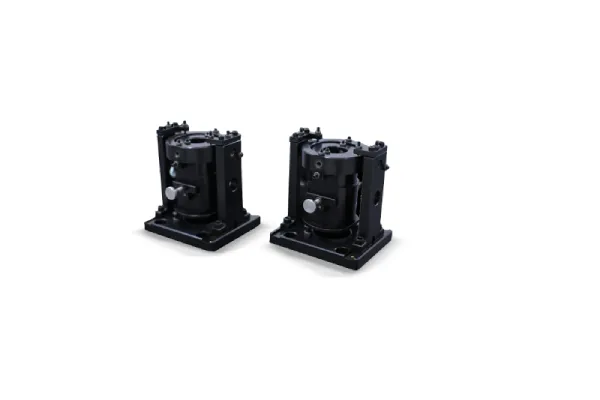
A combination of radial and axial floating provides maximum flexibility, ensuring precise honing by compensating for misalignments in both directions. This dual-floating fixture is ideal for applications requiring superior bore alignment correction and enhanced accuracy, making it a preferred choice for complex honing requirements.
Rotary Fixtures
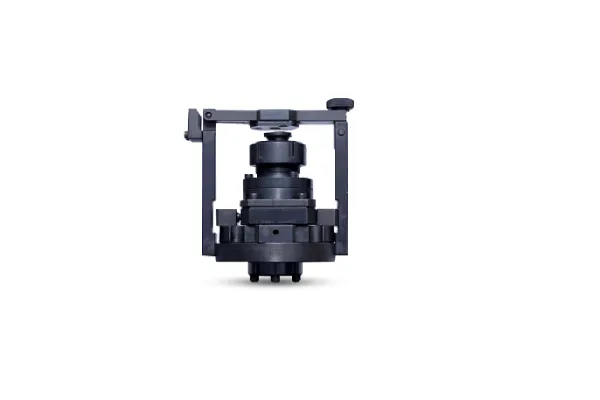
Rotary honing fixtures are used for rotating workpieces during the honing process, ensuring consistent contact with the honing tool and achieving uniform surface finishes.
Applications:
- Large-diameter bores in heavy machinery components.
- Automotive and diesel engine liners.
- Aerospace applications requiring uniform honing results.
Magnetic and Vacuum Fixtures
Magnetic and vacuum honing fixtures are used to hold non-ferrous or delicate workpieces securely without mechanical clamping, reducing deformation and ensuring a smooth finish.
Applications:
- Thin-walled or delicate materials.
- Precision honing of aluminium and composite materials.
- Workpieces where traditional clamping may cause distortion.
Choosing the Right Honing Fixture
Selecting the appropriate honing fixture depends on factors such as:
- Workpiece size, shape, and material.
- Required bore accuracy and surface finish.
- Production volume and automation level.
- Precision and alignment requirements.
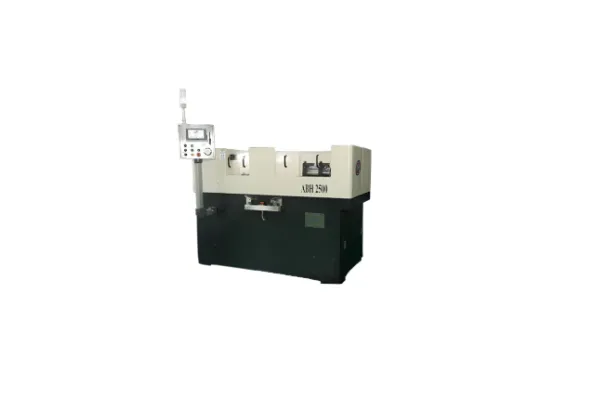
Types of Honing Machines
There are several types of honing machines, including:
Horizontal Honing Machines
These machines are ideal for long workpieces with precise bore requirements. For example, they are widely used in the automotive industry for honing engine cylinder liners to maintain consistent bore diameters and improve fuel efficiency.
Applications:
- Used for honing long cylindrical components such as engine blocks, hydraulic cylinders, and aerospace parts.
- Ideal for both through and blind bore applications.
- Common in the automotive, aerospace, and hydraulic industries.
Vertical Honing Machines
These are suitable for shorter components with varying bore diameters. They are commonly used for honing hydraulic and pneumatic cylinders, ensuring tight tolerances in aerospace and industrial applications.
Applications:
- Suitable for deep bores with high aspect ratios, such as hydraulic valves and gears.
- Used in industries requiring high precision, such as aerospace and oil & gas.
- Allows gravity-assisted honing, improving material removal efficiency.
CNC Honing Machines
Automated systems designed for high-precision, high- volume production. These machines are used in the medical sector to hone surgical instrument bores, ensuring smooth finishes for safe usage.
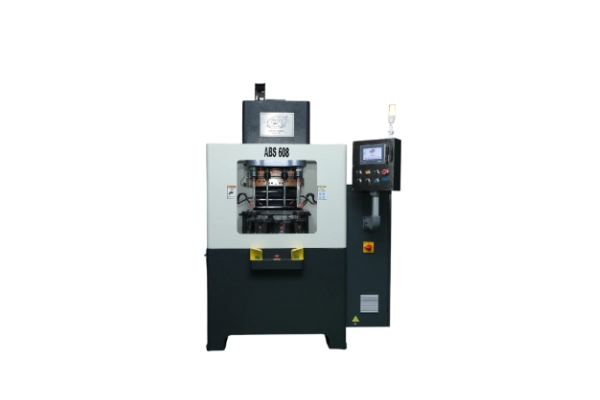
Application
- Used in industries requiring ultra-precise bore sizing, such as medical, aerospace, and automotive.
- Capable of achieving micron-level precision with minimal human intervention.
- Ideal for large-scale, high-volume production with strict tolerances.
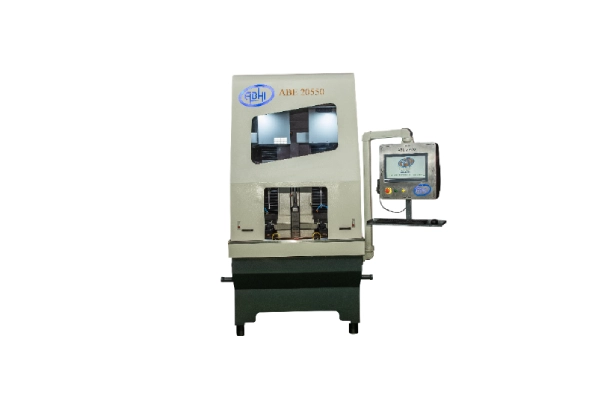
Manual Honing Machines
These are operator-controlled machines used for low- volume or custom applications. They provide flexibility in honing intricate parts, making them ideal for repair shops and specialized manufacturing units.
Applications:
- Used for small workshops, repair centers, and low-volume production.
- Suitable for honing small parts, such as gears and bushings.
- Requires skilled labour for consistent quality.
Choosing the Right Honing Machine
- Workpiece Dimensions, Shape, and Material
- Geometrical Parameter Requirements
- Cross Hatch Pattern Requirements
- Production Quantity
- Less Change Over Time
- Batch Size and Cycle Time
Comparison of Honing Machines: A Comprehensive Analysis
Feature | Horizontal Honing Machine | Vertical Honing Machine | CNC Honing Machine | Manual Honing Machine | Tube Honing Machine |
---|---|---|---|---|---|
Automation Level | Semi-automatic to fully automated | Semi-automatic to fully automated | Fully automated with real-time monitoring | Operator-controlled | Semi-automatic,specialized for long bores |
Ideal Workpiece Orientation | Cylindrical, longer workpieces | Compact and vertically aligned components | High-precision parts in varying sizes | Custom, repair-based workpieces | Long tubes, deep bores |
Bore Geometry Correction | Maintains roundness and straightness,effective for deep bores | Best for short bores with high alignment accuracy | Unmatched precision with micron-level adjustments | Operator-dependent,requires skill | Specially designed for long,deep holes |
Surface Finish Quality | Consistent, controlled finish | Superior finish due to gravity-assisted alignment | Ultra-precise,highly repeatable | Moderate, skill-dependent | Optimized for smooth deep bores |
Material Compatibility | Cast iron, steel, aluminium alloys | Steel, aluminium,hardened materials | Any material with programmable control | Various materials but requires skilled handling | High-strength alloys, hardened steels |
Production Efficiency | Medium to high,adaptable for various industries | High-speed operation, best for mass production | Extremely high throughput, ideal for large-scale industries | Low volume, best for specialized applications | Moderate,designed for deep bore honing |
Control System | PLC or motion-controlled automation | PLC-based control for consistency | CNC with adaptive feedback and self-correction | Manual adjustments by operator | PLC or servo-driven systems for precision |
Best Suited For | Automotive cylinder liners, hydraulic cylinders, aerospace shafts | Engine blocks,brake cylinders,aerospace, and medical parts | High-precision manufacturing,aerospace,defence, and medical applications | Tool and die making,maintenance, and small-batch production | Hydraulic cylinders, oil & gas industry pipes, aerospace structural tubes |
Cost Consideration | Moderate investment with versatile applications | Slightly higher cost due to precision mechanics | High initial investment but reduced long-term costs due to automation | Low initial cost but labour-intensive | High, due to specialized long-bore honing capability |
Conclusion
Honing is an essential machining process that enhances the precision and longevity of critical components across multiple industries. As technology advances, honing machines continue to evolve, offering increased efficiency, automation, and accuracy.
Understanding the honing process is crucial for manufacturers seeking to achieve superior surface finishes and optimal performance in their components. With the right honing equipment and expertise, industries can ensure the highest standards of quality and reliability in their products.
With over 29 years of expertise, Abhi Fine Products is a pioneer in honing technology, delivering high-performance honing machines that cater to a wide range of industries, including automotive, aerospace, hydraulics, defence, and medical manufacturing. Our commitment to precision, innovation, and reliability ensures that manufacturers achieve the highest standards of bore geometry, surface finish, and efficiency in their components.
Tell us how can we assist you?
We are always happy to answer any questions!
Just fill in the form and we will get back to you.
© 2025 All rights reserved. Abhi Fine Products.
Designed & Developed by Appac Mediatech Pvt Ltd